- Article is about History and Features of Banarasi Sarees, patterns-designs-types of zari, colours-price range and care guide.
Banarasi Silk (also known as Benarasi SIlk)
is a fine variant of silk originating from the city of Varanasi in Uttar
Pradesh, India. Saree woven from this fine silk, known as a Banarasi Silk
Saree is extremely popular all over India and the world.
With a mention in the Mahabharata and in the
Buddhist scriptures in the first millennium, Banarasi silk have its roots
seeped into the rich cultural history of India. Originally crafted exclusively
for the royalty, each Banarasi sari was created from real gold and silver
threads, taking as much as a year to make.
Reference
History of Banarasi silk sarees
The history of Indian sarees dates back to
the Itihasaas-Ramayana and Mahabharata in the 1000 to 300 B.C. “Varanasi was a well-known cotton weaving hub during the early Buddhist period.” Banarasi silk was introduced to India with the advent of the Mughal Empire. Note that brocade weaving gained prominence with the migration of weavers from Gujarat in the 17th century. The influx from Persia and Central Asia led to the
use of zari. Source
The Banarasi silk today is a maxiture of Indian and Mughal influences.
The art and culture of providing Banarasi
sarees with silks is very ancient. The continuations of passing down the
culture of artistry of the Banarasi saris from one generation to another have
never stopped. Persian motifs were mixed up with the designs of Indian silk for
creating this distinctive flowery pattern of Banarasi silk sarees, which are so
typical in present days.
Indian sarees are divided into two broad
categories, the traditional bridal and the designer segment. Banarasi
sarees are bridal sarees that are very popular because of their various
textures, colours, and designs.
Reference
and pic credits

Sources of Inspiration
Today Banarasi silk sarees are still considered to be one of finest traditional saris. It is well known for its designing and gold as well as silver brocade or the ‘Zari‘. The special characteristics of these sarees are their designs. Very often, they are decorated with intricate floral as well as foliate designs.
Moreover, you may also find a string of
upright leaves, which are called Jhallar.
The idiosyncratic features of these Banarasi silk sarees include heavy working
of gold, small detailed figures, metal visual effects and compact weaving as
well.
Reference
and pic credits
Features of Banarasi silk sarees
The Banarasi sarees are made in Varanasi,
Uttar Pradesh.
They are one of the finest traditional sarees
and very heavy due to its rich embroidery which makes them ideal for parties,
festivals, and weddings. This saree is traditionally made in four varieties
namely organza (Kora), Georgette saree, Shatir saree, and pure silk (Katan).
The many varieties of Banarasi silk saree are organza, satin borders, jangla,
Brocades, Tanchoi, cutwork, and Resham butidar that have interesting designs of
animals, birds, floral, fruit, human figures, and geometric patterns.
Persian motifs are also included in the
Indian designs to create distinct flower patterns of the saree used even today.
The Banarasi sarees were originally embellished with threads made from real
gold and silver for the royal family. For them to be affordable nowadays for
everyone, the threads have been replaced with coloured gold and silver threads.
This famous saree has eye-catching patterns and shades woven on a handloom and
shipped all over the world.
Reference
Making of a Banarasi saree
It usually takes around 15 to 30 days to weave
a Banarasi saree. However, it depends on the complexity of the design and
patterns. Normally 3 weavers are required in the creation of this saree. One
weaves the saree, the second one handles the revolving ring in making bundles,
and the third one assists in border designing. Making the Banarasi saree
requires teamwork. Ideally, a Banarasi saree has around 5600 thread wires and
all are 45 inches wide. The craftsmen make a base of 24-26 inches long.
Designing the motifs begins at the bundling stage.
An artist creates design boards by sketching
the designs on a graph paper along with colour concepts. Punch cards are then
created before selecting the final design. Next hundreds of perforated cards
are created to accommodate a single design for a saree. To knit the perforated
cards on the loom, different colours and threads are used. The perforated cards
are then paddled in a systematic manner to ensure the main weave picks up the
right colours and patterns.
Reference
Banarasi saree designs elaboration
The Banarasi saree is divided into categories like Tissue, Butidar, Cutwork, Tanchoi, and Jangal. Tissue sarees are woven with golden Zari Brocade to add sheen to the saree. The saree’s borders and pallu are patterned with self-woven paisleys. Butidar sarees are woven with brocade threads silver, silk, and gold. The darker shade of gold compared to the silver threads has earned the brocade patterning the name Ganga-Jumuna.
Cutwork sarees are the less expensive version of Jamdani sarees. They are products of the cutwork technique on plain
texture. Leaves, jasmine, creepers, and marigold flowers are popular motifs
featured on Cutwork sarees. Tanchoi sarees patterns are woven with
colourful weft silk yarns. The decorations on this saree are large motifs of
paisleys and the border has criss-cross patterns.
Jangal sarees are woven with colourful silk
threads and decorated with intricate patterns of Jangala motifs and vegetation
that fall along the saree. The luxurious fabric with intricate designs and
detailing makes this Banarasi saree ideal for weddings functions.
Reference and credits – All you wanted to know about this classic weave
The variegated patterns in detail
Brocade sari: The term
brocade refers to those textiles where patterns are created by transfixing or
thrusting the needle between thread patterns or the warp. The sari has multiple
motifs in gold and silver threads, used as extra weft against silk background.
The borders and pallav have scroll designs whereas the body of the sari can
have several appealing patterns throughout as per the designer.
Chiffon jamdani: Unlike the
other varieties of yarn in richer brocade saris, this kind has more coarse
twisted yarns that form the warp sheet. The S and Z warped ends are alternately
arranged that impart a wavy and crepe appearance to the textile. The jamdanis
generally have buti patterns all over.
Jangla: These are a must have wedding
trousseau item. These are rich and heavy due to the meena work, jaal and jangla
designs all over. The finish of the motifs is neat to resemble just the same on
both sides of the fabric due to swivel weave without any floats. Jangla sari
requires a minimum of two weavers who work together with 14 to 28 shuttles at a
time.
Kora cutwork: In this kind,
cut work are made against a plain ground. This gives a jamdani effect as the
loose thread dangling between the motifs are trimmed manually and neatly.
Resham buti: An affluent
kind of banarasi silk sari where butis are woven all over the ground bordered
with heavy design and highly ornate pallav.
Satin border sari: This
has pallav and border in satin weaves, the rest sari is plain.
Satin embossed sari: These have floral,
ilayechi and charkhana patterns all over in satin weave.
Tanchoi: The motifs are woven in satin weave
with silk as extra weft and are without zari. Its jamawar style and paisley
motifs are thickly spread throughout. These are quite heavy.
Tissue sari: These have
gold like appearance of cloth because they are woven with silk as warp and zari
running as weft with combination of zari and silk in extra weft. Therefore,
these are the most popular as wedding attire.
Various types of zari
a) Pure zari: The central part of pure zari
is made up of silk filaments, from which sericin has been removed. The silk
yarn is twisted in red or yellow hues, over which thin wire (lametta) of silver
and flatten wire (badla) is wound. The silver zari threads used in pure zari
are electroplated with great expertise in pure gold solution to produce good
quality gold zari.
b) Tested zari: Also available in the
market as imitation zari because it has the external quality of real zari and
therefore resembles real zari in terms of glimmer. This variety of zari is a
bit inferior to the real zari because of the use of copper lametta instead of
silver and silver embellishment is done on copper wire and to produce gold
zari, the tested zari is embellished with gold solution.
c) Powder zari: The mechanised process
followed for making powder zari is similar to the tested zari; it varies only
where the powder gilding is done on imitation zari instead of gold
electroplating.
d) Plastic zari: This is the most
inferior type of zari where plastic thread is used as lametta instead of copper
or silver.
Reference and
Good Blog
Motifs used in detail
There are umpteen motifs used. The designs
are of pretty floral pattern, vegetal designs, stylised dots, jal
patterns, asharfi motifs, geometrical motifs, small flower (buti), mango motif
(kalgha), human figures, bird depictions, animals and flourishing tree,
all drawn from nature. Some of the motifs on the walls of the temples in
Varanasi also find their presence on banarasi weaves.
Banaras silk sari is known for its softness,
glimmer and luxurious look. The sari achieves a majestic look through its rich
and intricate weave and zari work.
Reference and
pic credits
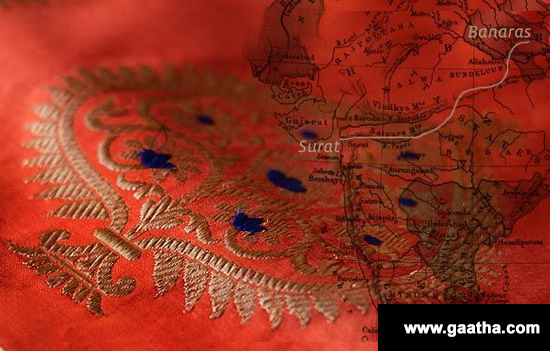
Dressing Banarasi Silk Sarees
A Banarasi Saree is a favourite among the
brides owing to its royal aura. Moreover, these saris have specific
geometric pattern which suit perfectly with joyous moments and celebrations.
Colours
Banarasi sarees are available in a host of
colours and are known more for the gold and silver zari work that adorns them.
Price range
A genuine Banarasi silk saree can be bought
for anywhere from Rs.3,000 to Rs.2,00,000 depending on the design and the
intricacy of the work. That said, a saree with a decent amount of work would
cost a minimum of Rs.8,000 to Rs.10,000.
Reference
Care guide
It is recommended that you dry clean Banarasi
sarees. However, if you choose to wash it at home, make sure to simply dip it
in cold water a few times before hanging out to drip-dry. Do not use detergent
in the first few washes and a clothes brush is an absolute no-no. You can
either wrap the saree in muslin cloth and store it away from sunlight or store
it in a hanging position in your cupboard. Either way, you must change the
folds every now and then.
Reference
Some fun facts about the Banarasi Silk Sarees
An ideal Banarasi saree has about 5600 thread
wires.
A single design of Banarasi saree required
hundreds of perforated cards to implement a unique design.
An authentic Banarasi saree takes about 15
days to 6 months to make. For even complex designs, more time is needed.
Ramayana and Mahabharata mention Banarasi
sarees.
Buddhist tales of Jataka and other texts also
mention about the exquisite weaves of Kashi.
In olden days, Banarasi silk sarees were made
only for royalty and the nobility. Silver and gold were used for weaving.
Banarasi saree is heavy because of the rich
embroidery and the zari work.
Banarasi Silk Sarees are considered to be
wedding trousseau in many Indian cultures.
The price range of a genuine Banarasi silk
saree (handloom made) can be somewhere between Rs 8,000 to Rs 3 lakhs. Anything
lesser than that has some quality compromised.
Reference
Conclusion
These traditional and stunning Banarasi silk
sarees are recognized globally due to the unique patterns and intricate designs
made on the sarees.
To see videos of how saris are made
1. Video 1 20 minutes
2. Video 2 Live History India 32 minutes – Nice
3. Video 3
short at 5 minutes
Author Trishna Patnaik is a self-taught
artist based in Mumbai, Trishna has been practising art for over 14 years. She
is now a full-time professional painter pursuing her passion to create and
explore to the fullest. She conducts painting workshops across India. She is
also an art therapist and healer who works with clients on a one to one basis.
Not to forget her quality writings on Indian Art and now Textiles for
esamskriti. She fancies the art of creative writing.
Designer Ritu Kumar wrote How
Chinese imports are destroying our traditional textiles
“I then studied Benaras silk saris for a few years in an effort to find out what had changed the saris radically from exotic, sexily-contoured unstitched garments to the present, stiff totally unwearable, saris which balloon out. It was incredible to discover that the reason was that the original yarns from Bhagalpur which were hand-spun, with no twist, called paat-baana, without which the beautiful masterpieces of Benaras could not have been woven, had been substituted by Chinese yarns.
We have indigenous mulberry silks from Karnataka, which are softer, finer, lighter and allow for more pliability when woven and have a wonderful texture. Organic ahimsa silks from the terai regions, India’s tussars and mogas, are an intrinsic part of our heritage. China dumped silk yarn in India at prices a fraction of their costs initially, and then slowly raised the prices to set up a lucrative business.”
Also see album of Sarees across India
1. Sualkuchi
Assam
2. Handloom Sarees of Orissa
3. Paithani
Maharashtra
4. Maheshwari
Madhya Pradesh
5. Chanderi
Madhya Pradesh
6. Bhujodi
Weaving Kutch
7. Patola
Weaves of Gujarat
The
purpose of this compilation is to document and promote. We have given credits
and reference links in this compilation along with third party links (to
promote). In case some are missed, it is not with malafide intent. Please
email full details to esamskriti108@gmail.com
and we shall effect the change.