- Read about the different type of handloom sarees of West Bengal with pictures.
West
Bengal has a rich saree making tradition. We present details of different type
of sarees.
Jamdani Saree

When one thinks of Bengal, one of the first things to pop up in our mind, right after the fish and sweets, is its thriving saree industry. Sarees form an integral part of every Bengali woman’s wardrobe and one of the most popular is the Jamdani saree.
Popularly known as Dhakai Jamdani or simply Dhakai, this art of textile weaving has its roots in Dhaka in modern day Bangladesh. Considered to be one of finest variety of muslin that is handwoven from cotton, the art flourished under Mughal patronage. Even the name, Jamdani, is of Persian origin and comes from the word “jam” meaning flower and “dani” meaning vase. The name is suggestive of the beautiful floral motifs on these sarees.
Weaving process
The
base fabric for Jamdani is unbleached cotton yarn and the design is woven using
bleached cotton yarns so that a light-and-dark effect is created. The process
is extremely time consuming as it involves a tedious form of hand looming.
Jamdani
weaving is somewhat like tapestry work, where small shuttles of colored, gold
or silver threads are passed through the weft. Designs range from the butidar, where the entire saree is
scattered with floral sprays, to diagonally-striped floral sprays or the tercha and a network of floral motifs
called jhalar.
Motifs
The
most remarkable part of the Jamdani weaving technique is that the motifs are
not sketched or outlined on the fabric. Instead, they are drawn on a
translucent graph paper and placed underneath the warp. Though Jamdani
technique is famous for sarees, it is also used to make scarves, handkerchiefs
and dupattas.
Popular
motifs include panna hajar (thousand
emeralds), kalka (paisley), butidar (small
flowers), fulwar (flowers arranged in straight rows), tersa (diagonal
patterns), jalar (motifs evenly covering the entire
saree), duria (polka spots) and charkona (rectangular
motifs).
Credits , Nice
colours and options , Wide variety
Baluchari Saree
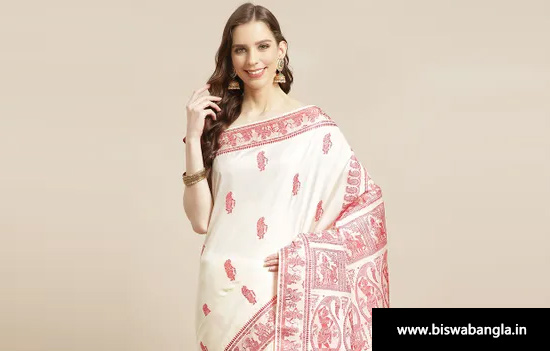
The
Baluchari sari traces its origin to West Bengal. The name Baluchari came into
existence because the weaving of these saris started in a small
village called Baluchar in the Murshidabad district of West Bengal
around 500 years ago.
Due
to some natural calamities, the weaving set up was then moved to
Bishnupur from Baluchar and the industry grew tremendously there
after the British rule.
Manufacturing
Baluchari sari is a time-consuming process. It requires extremely good
craftsmanship and takes around a week to weave one saree. These
are hand woven and use the purest of yarns depending on the material.
These were originally woven only using the purest of silk threads;
however, as time went by, cotton fabric was also used
to weave the Baluchari sari.
The mulberry silkworms
are cultivated through a process called sericulture and
the silk yarns are extracted from their cocoons.
These silk yarns are made smooth and colourful by boiling them in hot
water and soda, and then dyed with acid dye. After that, the yarn is
stretched to make it tight and strong enough to be woven into a saree.
The
complex yet beautiful process of weaving the motifs
and embroidery comes next. The raw designs are drawn on paper first
and then punched back into the sarees. The colours used these days,
while weaving Baluchari saris, are bright and cheerful.
A lot of
environment-friendly items are being used to weave Baluchari
sarees today. Banana plant stems, bamboo trees and natural products like
flower dye, fruits dye, neem leaves, turmeric leaves and dried twigs are used
in the weaving process.
Motifs: Themes and variety
Baluchari
saris today often have depictions from scenes of Mahabharata and Ramayana.
During the Mughal and British eras, they had a square design in the pallu
with paisley motifs in them and depicted scenes from the lives of the
Nawab of Bengal featuring women smoking hookahs, Nawabs driving horse
carriages, and even European officers of the East India Company. It would take
two craftsmen to work for almost a week to produce one sari. The main material
used is silk and the sari is polished after weaving.
While
there is not a lot of variation in the method
of weaving used today, Balucharis can be broadly categorised based on
the threads used in weaving the patterns as below:
Baluchari: The most
common Balucharis have threads in one or two colours to weave the
entire pattern.
Baluchari
(meenakari): Sometimes,
Balucharis have threads in one to two colours along with attractive meenakari
work in another colour that further brightens the pattern.
Swarnachari (Baluchari in
gold): Gorgeous Balucharis are woven with gold-coloured threads (sometimes
interspersed with a bit of silver) that illuminate the patterns to a much
larger extent.
Credits, See
this , Colourful
option
Linen Saree
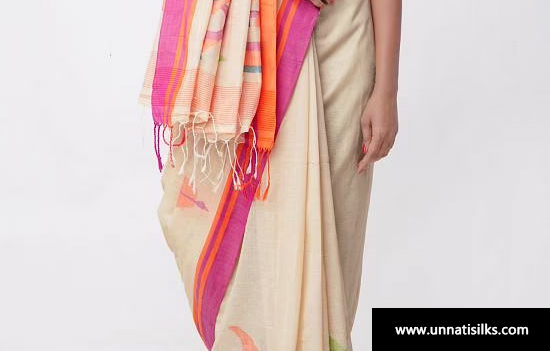
Linen
saree fibre is very absorbent. Lilen Sarees are valued for their exceptional
freshness. It makes for a beautiful colour combination lending it to be elegant,
comfortable and classy. Each saree is unique in its own way.
Pure Linen sarees have lustre and are hand-woven linen which are extremely soft. They have a fantastic fall and are known to accentuate a woman’s curves as they snug to the body.
Credits, Another
Option
Khesh Weaving
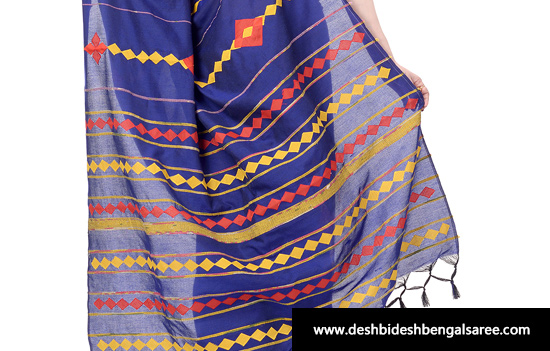
Khesh
weaving is a century old tradition practiced in Birbhum district of West
Bengal. It is a perfect example of sustainable fashion that involves recycling
and upcycling old fabrics.
In
Khesh weaving process, the warp is with the new yarn and the weft is with
strips of thin cloth obtained by tearing old sarees lengthwise. Though the
technique of khesh weaving is not new, using this technique to weave a saree is
only a few years old.
Khesh
sarees feel soft in texture but is coarse at places. It is extremely
comfortable, effortless and breathable in summer and warm for a light winter.
Some Khesh sarees are just plain and some do come with additional work like
kantha, applique, mirror, block print and batik print.
Credits, Good
Blog
Phulia Saree
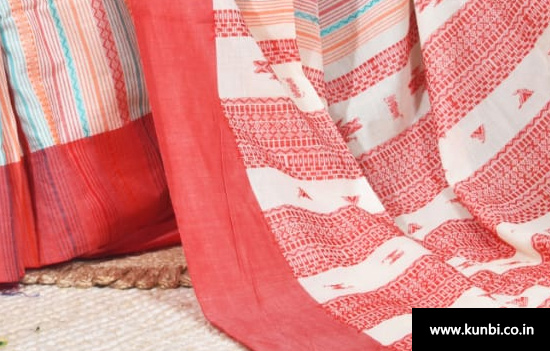
These
light cotton sarees from Phulia in Bengal are sure to brighten up the wardrobe.
Pleat it up for a formal occasion, throw it over the shoulder say for a brunch
with the girls and accessorise it depending on the mood. Whatever you do you
will revel in the softness of the cotton and be energised by the bright
colours.
Once
the poster village of West Bengal handlooms, life for weavers here in Phulia is
now a constant struggle. Phulia is famous for its Tangail saris, similar to the Dhaka Jamdani in technique but softer
in feel, with the motifs spaced out. The Phulia Tangail is woven in silk as
well as cotton.
Credits , Another
option
Begumpuri Sarees
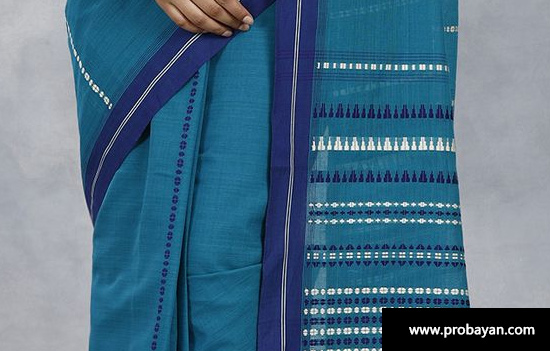
Begampur
is a small but well-known village in Chanditala II block, Hooghly district
in West Bengal. It is 30 km away from Kolkata.
Handloom
weaving is the main occupation in this village. The number of handloom weavers
has dwindled from about 4000 in last decade to about approximately 2000 now,
due to migration to another profession.
For
a long time handloom weavers were producing a well-known sari variety, locally
known as matapar saris which means
simple border without any ornamentation, woven with coarser cotton yarn (40s x
40s & 40s x60s). These cheaper variety of saris are mainly of coloured
stripes and check patterns and with designs in the borders.
After
the cluster intervention, weavers were imparted training in Designing, Dyeing,
Preparatory processes like drum warping, sizing etc. and importantly, in dobby
and jacquard weaving with the intent of producing diversified products. Weavers
improved their skills and started producing new varieties of quality cotton
sarees by adopting new techniques and modifications taught to them.
Materials used
Normally,
40s to 100s count of cotton yarns are used for Begampuri sarees both for warp
and weft. Steel reeds of 56s to 76s are commonly used to keep the texture of
the sarees at par with Dhaniakhali gharana. The picks per inch are almost equal
to ends per inch. As a result, balanced texture is obtained which gives comfort
in wearing.
Wooden
Dobbies are widely used for extra warp designs and jacquards are also in use at
present.
Weaving technique
Begampuri
sarees are woven in balanced texture with contrasting borders in red, black,
purple, orange etc., emphasized by a serrated edge motif. Narrow to broader
borders is woven with designs of variety of stripes and figured motifs using
dyed cotton yarn. These broad borders known as Maathapaar or Beluaaripaar
were often in two colours- such as black and red with a compact weave thus
making it harder.
Hank
yarn sizing is in practice in Begampur. The starch used for sizing are mainly
sage, arrowroot, rice, wheat, parched rice (Khai) etc. Sectional warping
machine is used to for warping replacing age old street warping. Local wooden
dobby of capacity up to 60 levers is normally used on pit loom or frame loom
for weaving Begampuri Saree with extra warp of 2/100s or 2/80s cotton yarn.
The
Begumpuri cluster, named after the eponymous Begumpur in Hoogly district of
West Bengal, is well known for its bright and colourful combinations, intricate
stripes and the serrated extra weft border designs.
Credits , Another
option
TANT saree
It is mainly
in cotton, woven in modern day Bangladesh and West Bengal. Also known as
Jamdani tant, the weaving of this saree flourished during Mughal era.
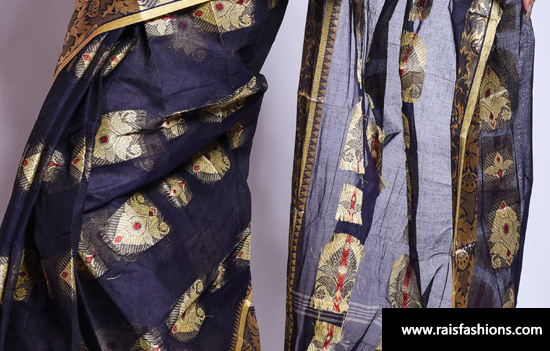
It
became so famous during British rule that the British government tried to
minimize its production to save their textile industry.
Weavers
continued weaving this style of saree and today, Tant sarees are one of the
most popular styles of Bengal sarees.
The
cotton thread is intricately woven into a Tant Saree by expert craftsmen. The
borders are woven a little thick, making it less resistant to getting worn
out.
Typically,
a Tant saree comes in pastel shades with beautiful thick borders. Florals and
Paisley motifs are often used on a Tant Saree.
With
attractive borders, hand-woven traditional as well as fancy motifs, exquisite
embroidery-work and sometimes exotic hand-painted tribal art, the comfortable
Bengal cotton sarees also make it a perfect daily wear.
Weaving Technique
Bundles
of cotton threads coming from the mills are first washed to remove any
chemicals, sun-dried, bleached, again dried, and then dipped in boiling
coloured water to dye them. They are then starched and processed some more to
make them finer and stronger. The threads are wound on bamboo drums to feed
them into the loom for weaving.
Every tant saree is characterized by the design on its border, pallu and body. These
designs are drawn by an artist and transcribed onto soft cardboards by
perforating them which are then suspended from the loom. Now all is in place
for the weaving to begin. The simplest of tant sarees take about 10-12 hours to
weave. More intricate designs could even take 5-6 days to complete a saree.
Types
Tant sarees can be classified based on the
region where they are woven, or the motifs depicted on the sarees. The major
regions of tant production in West Bengal today are:
Fulia and Shantipur (in Nadia): Combining the weaving styles of the original Shantipur weavers and the migrant weavers from Tangail who settled in Fulia, this region has developed the “Fulia Tangail” style of weaving and produces among the best quality tant sarees today. These tants are soft and fine in texture, come in vibrant colours and have large, intricately woven motifs.
Dhaniakhali (or Dhonekhali in
Hooghly): Tant sarees from this region are of good quality, mainly come in
pastel shades and have striped patterns and fewer motifs.
Begampur (in Hooghly): Begampur
specializes in loosely woven, light-weight and translucent sarees in deep,
bright colours.
Kalna (in Burdwan): Tants
from this region are based on the Tangail style of weaving.
Atpur (in Hooghly): This
town was known for producing coarser sarees and dhotis for everyday wear. The
term Atpoure which means “common wear” denotes the Bengali style of wearing sarees which used to be the traditional way of draping for women of this region.
A variety of traditional motifs are
woven in the borders and pallu of the tant sarees. Some of the popular ones
are: bhomra (bumble bee), tabij (amulet), rajmahal (royal palace),
ardha-chandra (half-moon), chandmala (garland of moons), ansh (fish scale),
hathi (elephant), nilambari (blue sky), ratan chokh (gem-eyed), benki (spiral),
tara (star), kalka (paisley) and phool (flower).
Good
read , Credits
Dhaniakhali Saree
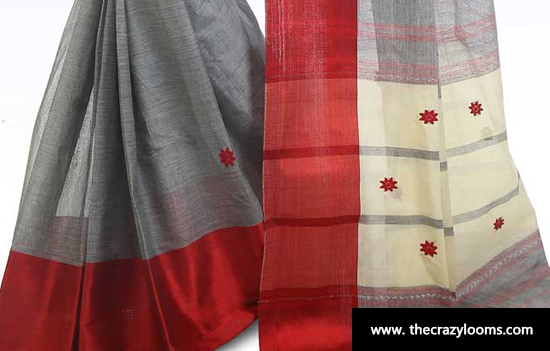
One
of the most beloved traditional handloom sarees of West Bengal is Dhaniakhali
saree deriving its name from the place Dhaniakhali in Chinsurah subdivision in
Hooghly district. Hooghly district is home to some of the oldest cottage
industries like silk and cotton handloom weaving, brass and bell metal
manufacturing, oil pressing, village tanning and others.
Dhaniakhali saree is often called as the ‘golden crop’ of handloom sarees. It is extremely popular for its rich colourful combination, compactness, design, colour fastness and long-lasting property. Dhaniakhali was well-known for its superfine cotton dhotis but as the demand decreased, the weavers took to weaving sarees. The sarees underwent a gradual change from narrow borders and jalchuri of dhotis to a more modern dobby and jacquard system to incorporate contemporary themes, motifs and patterns.
A
plain coloured border called matha paar or beluaari paar with a tooth-like formation warp (lengthwise
yarns) woven on the upper edge of the border is one of the earliest types of
Dhaniakhali saree. Lal border (red border), lal daant
paar (red tooth-edged design), pota
maach dure (fish pattern on both border and body), pota barfi
daant dure (tooth and diamond pattern on body and border), Muga dure phool paar dure (Muga
silk stripe with flower border), Muga kalka paar (Muga with paisley
border), Ganga Joli (off-white stripes in the body with an extra warp
two band border on either side) and Kalaka paar dhakka (paisley
border with receding body stripes) are some of the oldest types of Dhaniakhali
sarees.
Later
on latapata (creeper), narkel phool (coconut
flower), kalka paisley and others made their way into the border.
Dhaniakhali saree in its present form is woven in flying shuttle or pit loom
using 80 feet/100 feet cotton yarn in warp (lengthwise yarns) and weft
(crosswise yarns).
A local bamboo reed called Sar is used in the weaving of the saree to group two warp
threads. It gives flexibility and desired texture. Hank yarn sizing is adopted
here and the starch for sizing contains sago, arrowroot, rice, wheat, puffed
paddy etc. Denting order of special types like 3 ends per dent followed by 2
ends per dent and 3 ends per dent followed by leaving a dent blank makes for
aesthetically pleasing designs. The picks per inch (number of weft threads per
inch of woven fabric) is always more than the ends per inch (number of
warp threads per inch of woven fabric) which is the most unique trait
of this saree.
Extra
warp designs like floral, abstract, historical backgrounds, temples, colour
patterns, buttis and others are produced using dobby or
jacquard method. Dhaniakhali saree has kheju churi design thread
arrangement (braid of special weft threads of twisted cotton yarns in two
colours) woven in the pallu which is more prominent than those seen
in other Bengal sarees.
Credits , Another
option
The
purpose of this compilation is to document and promote. We have given credits
and reference links in this compilation along with third party links (to
promote). In case some are missed, it is not with malafide intent. Please
email full details to esamskriti108@gmail.com and we shall effect the change.
To read all
articles by author
To
read all articles on Traditional Indian Textiles of India
Author Trishna
Patnaik
is a self-taught
artist based in Mumbai, Trishna has been practising art for over 14 years. She
is now a full-time professional painter pursuing her passion to create and
explore to the fullest. She conducts painting workshops across India. She is
also an art therapist and healer who works with clients on a one to one basis.
Not to forget her quality writings on Indian Art and now Textiles for
esamskriti. She fancies the art of creative writing.