- This article covers handlooms in Madhya Pradesh (Bagh Print, Maheshwari and Chanderi and Indori Sarees), Rajasthan (Kota Duria, Pattu Weaving, Zardosi) and Chhattisgarh (Kosa Silk saree).
Known as the ‘Heart
of India’ Madhya Pradesh is well known for its culture, monuments and wildlife.
Though the state has some cultural similarities to states like Rajasthan and
Maharashtra, it is still unique. Handicrafts of Madhya Pradesh are well sought
after owing to their intricate designing. The state has rich tribal traditions
as well.
This diversity in
communities has given Madhya Pradesh a unique culture which can be titled as
traditional and ethnic. A prominent element of Madhya Pradesh’s culture is its
traditional clothing.
This article covers
handlooms in Madhya Pradesh (Bagh Print, Maheshwari and Chanderi and Indori
Sarees), Rajasthan (Kota Duria, Pattu Weaving, Zardosi) and Chhattisgarh (Kosa
Silk saree).
Madhya Pradesh
1. Bagh Printing from Madhya Pradesh
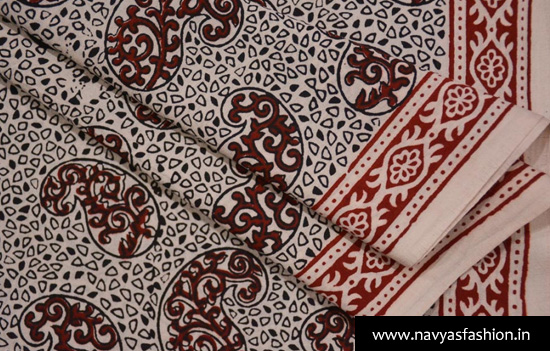
History
Bagh is
a small town in Madhya Pradesh popular for its hand-block printed textiles. A
saying goes that the town got its name from the tigers (known as Bagh in Hindi)
that once wandered the area. Originally, tribal residents were the only ones
who wore these Bagh patterned clothes.
A
Bagh printed outfit is easily identified by a simple outline motif in black and
red. The beauty of this print is that it is hand-printed using only natural
dyes and traditional designs. The printing is largely done by the Khatri
community who are believed to have brought this craft from Sindh 400 years
ago.
Blocks
The Bagh printers use high-quality woods such as Sagwan and Sheesham. An intriguing story is that the Khatri's have thousands of blocks that are inherited across generations and preserved separately and meticulously maintained, even if damaged or broken.
Bagh Designs
Geometrical
and floral designs are alternatively printed in red and black dyes on a white
backdrop. The most popular motifs of Bagh are flowers, mango, coconut, zig-zag
lines and honey bees. Chain or anklet designs are some commonly used designs in
the borders.
The
native people traditionally wore odhani and lugdas (sarees) made from the Bagh
printed fabrics. However, to meet customer demand, these prints are now also
seen bedsheets, table cloths, cushion covers and handkerchiefs.
Process
The
Bagh printing process is time-consuming and involves six stages –
1. Preparing the fabric
The
fabric is soaked for 2 hours and thoroughly washed to remove starch and later
sun-dried.
2. Myrobalan treatment
The
fabric is soaked overnight in salt, castor oil, goat droppings and then washed,
dried. This step is repeated a couple of times till the fabric becomes soft and
absorbent. It is then treated with Myrobalan for ten minutes, which gives the
yellow colour to the cotton fabric and aids the dye uptake later.
3. Printing of Mordants
The
printing pastes used are usually in red and black colour which uses alum and
iron sulphate as mordants respectively. Instead of glue, these paints are mixed
with chiyan (tamarind seed powder) to
get a perfect consistency. The printing is carried out by meticulously stamping
small hand blocks usually square or rectangular in shape.
It
takes around three hours to print one saree. After printing, the fabric is
allowed to dry thoroughly and then kept away for fifteen days so that the dye is
properly absorbed by the fabric.
4. Washing
Now,
the mordant-printed fabric is rinsed to take off any leftover gum or mordant by
soaking it in water for twenty minutes or pounding it on a stone. If this step
is not carried out properly, stains will appear in the finished fabric.
5. Application of red dye
After
washing, the cloth is boiled with alizarine and dhawada ka phul in a copper
vessel. Once it dries, you will notice that the areas printed with iron paste
turn black and the alum printed parts develop a reddish maroon colour.
6. Final Wash
After
drying, the fabric is washed again 3-4 times. This process is
called tapai. Each block print is unique. Bagh printing definitely has a
special place in our history and heart.
Read good
blog, Credits , insightful
blog
2. Maheshwari Saree
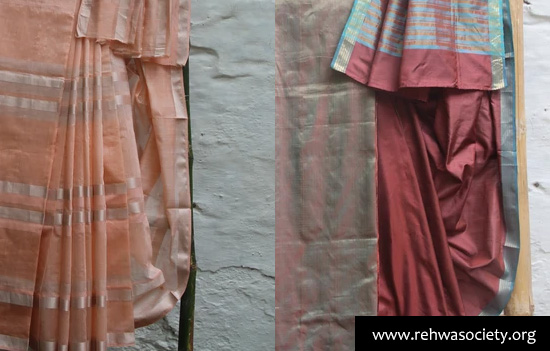
On
the banks of sacred Narmada river, lies the town of Maheshwar. It was
ruled by the Holkars, has a fort-numerous temples and a ghat. It attracts
tourists the year round and is known for its weavers.
Maheshwari
- one of the oldest handlooms! Maheshwar is best known for being the hub of
handloom weaving since the 5th century, but it gained fame during the rule of
Rani Ahilyabai Holkar (1767-1795). The delicate Maheshwari fabric is woven with
silk and cotton yarns, which gives it a soft texture and makes it a perfect
summer textile.
Loom Rehwa Society Maheshwar.
It
is assumed that the very first Maheshwari sari was designed by Ahilya
Bai. The queen, in 1760, asked talented handloom weavers from Surat and Mandu
to work for her empire. They were appointed to prepare turban fabric and
exclusive nine-yard nauvari saris which would be worn by the females of Malwa
court and used for the gifting purpose to the royal guests. Well-known for
being subtle and rich in quality, Maheshwari saris have always exuded dignity
and elegance!
The recent revival of Maheshwari started with the establishment
of Rehwa Society.
Due
to the advent of factories, new and inexpensive clothes in the market,
gradually the weaving tradition dropped! The revival of Maheshwari saris is
credited to the members of royal family including Richard Holkar and Sally
Holkar, son and daughter-in-law of Maharaja Yeshwant Rao Holkar II. In 1979,
the couple formed a non-profit organization called Rehwa Society to provide
employment to women and revive the centuries-old institution of handwoven
Maheshwari saris, dupattas and dress material. The society has
approximately 250 weavers and over 1500 looms today.
Salwar, Hansa Creations Maheshwar.
The unique designs and patterns of Maheshwari saris
Earlier,
the Maheshwari saris were made of finest cotton yarns with motifs inspired from
the intricacies engraved on the Maheshwar fort and temples. Today, the fabric
used in the sari is weaved using a blend of Coimbatore cotton and Bangalore
silk yarns with some new-fangled and more graceful motifs such as rui phool
(cotton flower), chameli (jasmine), hans (swan) and heera (diamond) embossed on it. The sari comes with a reversible
border and the unique five stripes on pallu or aanchal. Nevertheless, the
border is usually made with zari thread which is sourced from Surat. Some of
the colours used in weaving are tapkeer
(deep brown), aamras (golden yellow)
and angoori (grape green).
A
sari takes 3-10 days to complete, depending on the design. The most
time-consuming part of weaving is the making of pallu or aanchal which can take
3-4 days because it entails more detailed designs.
Regardless
of its simple style many popular designers and fashion houses are incorporating
Maheshwari fabric and sari to their collection.
Despite
their subtle and simple style, Maheshwari saris exude charm and sophistication.
Silk thread is used in the warp (tana), and cotton in the
weft (bana), imparting to the fabric, a lovely, silken sheen. It is light
and comfortable to drape, an ideal choice in the region’s hot weather.
The
uniqueness of Maheshwari saris lies in the weave. The body of the sari has
small checks, stripes, or can be plain, but the typically
striped pallu and border designs are inspired by traditional motifs,
or architectural embellishments found in the town’s temples and monuments.
The
centuries-old handloom weaving tradition is practiced in almost every Maheshwar
household.
Introduction and History Rehwa
Society Maheshwar products , Discover
Maheswaris the Rehwa way , Making
of Maheshwari Saris at Rehwa , Maheshwari
Sarees Maheshwar Album
3. Chanderi Sarees
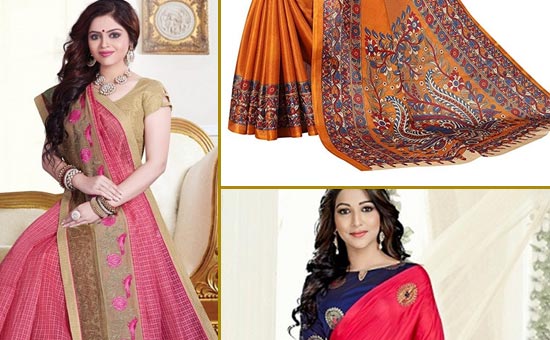
Chanderi
Sarees and their Rich History
How
to Identify and Differentiate between Maheshwari and Chanderi Sarees
4. Indori Saree
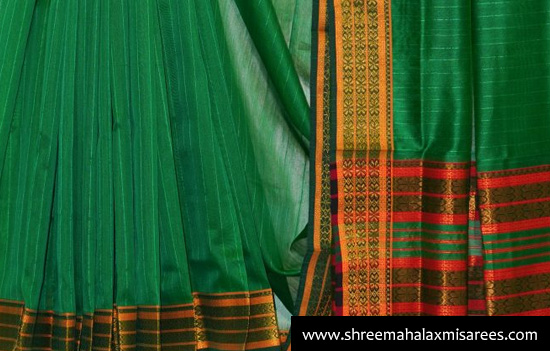
The
pallu is done up in bright colors like magenta, pink, green, mauve, violet and
maroon for the Indori Saree. These sarees are known for their unique pallu
which are made five stripes, three colored and two white alternating, running
along its width. There are only a handful of craftsmen who weave the
original striped designs of the sari making for the Indori Saree.
There
are 5 major categories namely, ‘Chandrakala, Baingani Chandrakala, Chandratara,
Beli and Parbi. The Chandrakala and Baingani Chandrakala are the plain kind,
whereas the Chandratara, Beli and Parbi fall under the striped or checked
technique. Neem-reshmi is a variation of silk checks on a cotton ground, both
in the warp and weft.
Credits There are sarees made in Jhansi too but they are rare.
Rajasthan
Rajasthan’s textiles represent an amalgamation of
generations of experimentation with fabric, handicraft skills and a sharp eye
for detail. These textiles, woven with incredible precision, are the result of
an oral tradition that has passed down generations, and honed with finesse and
purpose. It is always advisable to “buy local” – i.e. visit small villages
instead of buying from Rajasthan’s urban shopping centers, as this is where you
can get the kind of fabric, weaving and embroidery that is impossible to get
anywhere else in the world.
5. Kota Duria
Kota Duria Cotton Zari sari.
Kota
Doria or Kota Doriya is the name of a light woven fabric made of
tiny woven squares (khat) which is
still handwoven on traditional pit looms in Kaithoon near Kota in Rajasthan and
in some of the surrounding villages. Kota Doriya Sarees are made of pure cotton
and silk and have square like patterns known as khats on them. The chequered
weave of a Kota sari is very popular. They are very fine weaves and weigh very
little.
History
It
is said that Rao Kishore Singh of Kota brought weavers from Mysore in Karnataka
to Kota in the mid-17th century, as they wove a characteristic small squared
lightweight cotton fabric that looks like graph paper and is suitable for
turbans. Rao Kishore Singh died in a battle in Karnataka in 1696 while fighting
for the Mughal Emperor Aurangzeb.
The beauty of Kota Doria
Kota
Doria is a one-of-a-kind hand-woven fabric with a distinctive square-checkered
pattern. The exquisite quality of the yarn, its agility and softness, which are
created by polishing the warp yarn with a particular starch or kanji, are the
distinguishing features of this fabric. Different counts of cotton yarns or a
blend of silk and cotton yarns are differentially woven to create the checkered
pattern.
Weaving
with silk is a very unique and different type of weaving in which cotton and
silk threads are combined in both the warp and weft directions. This results in
the development of squares, which are referred to as khat. The khats
are referred to by many names such as khan, charkhana,
chokhdi, and checks in various parts of the world.
This weaving procedure is not followed by any other handloom
textile in India.
Motifs
The
popular motifs used are keri (mango), phool patti (flowers with petals
and leaves), chokdi (checks), ginni (coin), paan (leaf), shakarpara (sweet) and geometrical motifs.
Colours
Since
this transparent lightweight fabric is suitable for summer, light pastel shades
of yellow, green, pink, red and orange are used by weavers. For the motifs,
darker colours such as blue, green, pink and yellow are popular.
Weaving Process
Throw-shuttle
pit looms were employed in the past. Frame looms and jacquard looms, on the
other hand, have become more popular in the production of sarees with woven
borders and motifs in recent years. The wrapping, dyeing, sizing, winding and
weaving is done by weavers with the help of their family members.
After
warping, the cotton yarns remain brittle and they are made strong and smooth by
sizing them. A liquid made of arrowroot, wheat flour, rice and wild onions, is
applied to size it. After sizing the yarns are warped and wound on the warp
beam of the loom. The majority of the weavers use unbleached yarns, and the
dyeing of the fabric is done after weaving. Direct and reactive dyes are used
for dyeing yarns.
In
the present day, this versatile and lightweight ensemble is an integral part of
occasion wear and wedding trousseau.
Credits
6. Pattu Weaving
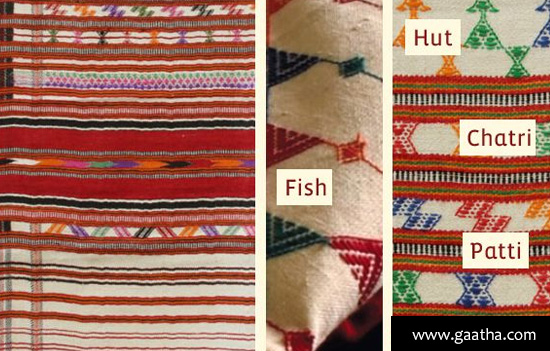
Pattu
Weaving is very popular throughout Rajasthan and it is a type of general
weaving. Pattu weaving is used a lot in Rajasthan and other parts of the
Western India. Western Rajasthan has special importance for pattu weaving where
you can find its made blanket, shawls and pattu or patti which is a narrow
strip of cloth.
The
traditional pattu wears can be found in Barmer, Jaisalmer and nearby villages.
Sheep and camel wool found in natural cream color, black and brown are widely
used for weaving pattu. The usages of cotton fiber and synthetic dyes have
included others such as orange, bright red, blue, pink, green and
saffron.
Fabric
is used in twill weave on pit loom and numerous methods are produced through
the interlocking techniques and additional weft figuring. In warping, different
kinds of vertical warp bands in complementary colors are included on both sides
of the loom and then the technique of interlocking is employed to obtain the
pure color. Bobbin contains a weft in similar color as the separate band,
applied of weaving the restricted parts of bands.
Additional
weft calculating that carried around embroidery looking on loom. It appears
beautiful on the clothing. The additional weft is added on a small size of
stick which is passed amid a bare minimum of 2 and a maximum level of 12 picks.
The craftsman picks up the warp yarns and passes it to put in the additional
weft yarn.
The
Meghwal community in Rajasthan specialise in making a wide range of pattus such
as kashida pattu, baladi check and hiravali pattu. Other 2 popular designs made
in this region are malani and bhojsari. Weavers in Rajasthan use the
similar pattern for producing woollen dhabla and other types of lower garments
for Kumhar and Gujar women.
Motifs
have a special geometric way. A wide range of articles and the floor and wall
paintings are known as mandana. All pattus have a feature connected in the
centre part. There are 2 strips connected to make the pattu available for both
men and women. Colorful and bright pattu is warm and large enough to easily
drape the body. Shepherds, farmers, and other people use it widely in the
villages of Rajasthan esp. in the winter season.
Pattu
Weaving in Rajasthan , Credits
Jhiri Handloom Weaving is rare. Good
blog
, Jhiri
Handloom Cotton , Nice design Cotton
Sarees
7. Zardozi
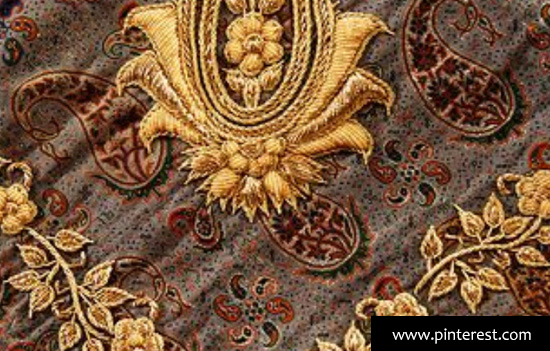
Zari
or Zari Work as it is known, is an intricate art of weaving threads made of
fine gold or silver. These threads are further woven into fabrics, primarily
made of silk to create intricate patterns. The designs are so exquisite that
apart from the monetary value attached to these threads, the fabric also gets
an overall rich look.
Origin and History of Zari Work
It
is believed that the word Zari originated in a village by the same name in
ancient Persia (Iran of today) where artisans used the skill of weaving thin
threads of gold and silver onto fine fabrics of silk. The art was brought to
India by Persian migrants between 1700-1100 BC. However, zari work flourished
during the Mughal era esp. under the patronage of Emperor Akbar.
Sources of Inspiration
Elegance
is what lies in the intricate patterns of Zari work. If we trace the actual
inspiration behind this technique, it would take us to the medieval times where
Zari was used on silk fabric. The patterns were inspired by ancient beliefs and
rituals but they vary from place to place and are passed down over the
centuries.
The Making
Zari
is produced by twisting a flattened metallic strip made from pure gold, silver
or a metallic polyester film around a yarn made of silk, cotton, polyester etc.
These zari threads are processed to increase the brightness of gold plating,
giving it an aesthetic look.
Faces behind the Zari Work
The
intricate art of Zari is passed down from generation to generation and is
protected by a few only. Zari work is the result of amazing talent &
needlework. The artisans sit on the floor behind the equipment working on a
piece of saree or suit. The speed at which they do the task is simply amazing. Kinari work done by men & women of the
Muslim community also formed the original faces behind this art form redefining
the essence of traditional artistry.
Variety
Zari,
which once enjoyed a lot of royal patronage, has slid down due to high costs of
precious metals such as gold and silver. In keeping with the times and in a bid
to appeal to various income groups, Zari has gone through some changes and
extensions.
Zari is
categorized into 3 types:
1. Real
Zari: It is made of pure gold & silver. Due to the high cost
of pure gold and silver, Real Zari is sought after by the very rich.
2. Imitation
Zari: It is made of silver electroplated (thinly) copper
wire. Imitation Zari was used as a replacement for silver. However with
increasing prices of copper, even Imitation Zari is produced in a rather
limited way.
3. Metallic
Zari: It is made of slitted polyester metallized film. Metallic
Zari is the work which is in vogue as it weighs quite lightly compared to pure
gold and silver or for that matter copper. It is also affordable and more
durable compared to Real Zari and Imitation Zari.
Clothes
with Zari are generally made-to-order in case of Real or Imitation Zari,
whereas Metallic Zari can be bought off the shelf.
Wearing Zari Work Attire
Sarees,
kurtas and salwars with zari are essentially worn during very special occasions
such as weddings. Fabrics with Zari lend a regal look.
Art Silk Zari Woven Saree
Zari
work lehengas are the essence of bridal trousseau. They are known for the
refined work, exquisite patterns and exceptional grace.
Maintenance
Zari
contains the weaves of gold and silver. The metal esp. the silver weaves react
to the atmospheric air and looks dull & old. To maintain its shine, the best
thing is to wrap them in soft cotton or a muslin dhoti. This prevents them from
any reaction.
Dry
cleaning is the best for Zari embroidered dresses. If there is a need to wash
these dresses, it should be done in mild soap water, then dry these in shade.
It is also advisable to avoid spraying perfumes or deodorants directly on these
dresses.
Credits
8. Kosa Silk Chhattisgarh
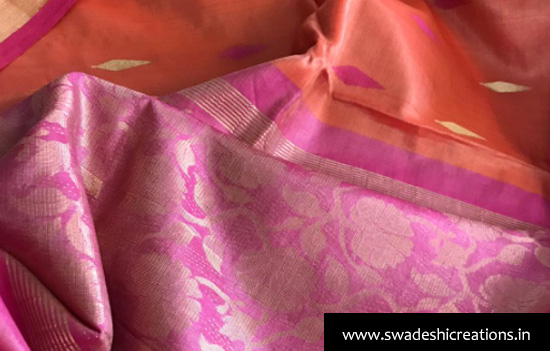
Chhattisgarh is one
of the 28 states of India. The textiles here are woven in heavy cotton. Keeping
the public demand saris are now also being woven in finer counts as well as
combination weaving of cotton and tussar. Traditional way of weaving on manual
looms is followed in Bastar having motifs of birds, lions bows, animals,
arrows, huts, peacocks, pitchers, temples and tribal flowers. These fabrics are
worn by adivasis on auspicious of festivals, marriages and dances.
Kosa
silk is obtained from an Indian silkworm – Antheraea mylitta and is a variety of
Tussar silk. It is drawn out of cocoons which are especially grown on specific
trees known as Arjun, Saja and Sal. Kosa silk is known for its sturdiness and
is preferred to pure silk in Chhattisgarh.
The
tribal, forest origins of the Kosa silk saree have greatly influenced the kinds
of nature inspired designs seen on it. This saree is highly in demand across
India and the world. It is available in both traditional and modern varieties. To
this date, this fabric is exclusively produced in India.
Unique & Truly Indian Fabric
The
main distinguishing factor of the Kosa silk fabric is that it is produced using
threads from a special type of silk worm called Kosa which is specially grown
in Arjun, Saja or Sal trees in forests in the center of India.
The
threads thus produced are quite coarse in their texture but it is this
coarseness that sets them apart and hand-woven, pure Kosa sarees are often
priced higher than the fine silk versions.
Kosa silk sarees
The
beautiful Kosa silk sarees are not only distinguished by the heavy, bumpy yet
graceful look of the fabric but they are also known for the beauty of the
designs woven into them.
Typical
patterns such as the Jaala (net) and Fera weave patterns are often used in
these sarees to create unique, artistic designs inspired by natural scenes
(especially those from the forests), tribal tales and mythological stories. The
contrast of the rich gold shade of the original fabric against the bright
natural dyes used for the designs and patterns creates an attractive aesthetic
effect for the sari and really sets it apart from any other type of silk
saree.
Nowadays,
all types of modern and ethnic designs from other parts of the country are used
to decorate Kosa silk sarees, creating a vast range for women to choose from.
Types of Kosa Silk Sarees
The
Kosa worm is quite rare and the cultivation of it is very labour intensive
which is why many Kosa saree types are woven in combination with cotton or
polyester threads to bring down the cost of the garment. When it comes to the
highly coveted Kosa silk, Chhattisgarh is the main center of production.
It
is considered a sub-type of Tussar silk, though it has several distinguishing
characteristics which have made it an extremely popular sari fabric. The sarees
made with this fabric are known for their distinctive, uneven texture and pure
quality.
The
classic Kosa saree comes in natural shades like pale gold, fawn, cream, honey,
orange and so on. Natural dyes are used to create interesting designs and/or to
dye the entire Kosa saree. These include colors like yellow, sourced from the
fire flower and deep red from Lac. Nowadays, of course, chemical dyes are
widely employed to dye these saris in a wider range of colors such as blue,
purple, green etc.
Wearing the saree on weddings or traditional occasions
Kosa
sarees are considered auspicious, traditional saris in the region where they
are produced and are therefore the number one choice for important functions
and ceremonies such as weddings, festivals and celebrations. Many women
consider these a great ceremonial or festival wear option because of their
combination of beauty, comfort and traditional designs.
The
best way to accessorize Kosa silk sarees is with traditional Indian jewellery.
The tribal vibe of these garments will also match well with funky tribal
necklaces, dokra earrings, beaded jewellery sets and oxidized silver bangles.
Credits , for Kosa
Silk Sarees , Kosa
Silk brightening up lives of Weavers
To
read about Bastar Craft and Culture
The
purpose of this compilation is to document and promote. We have given credits
and reference links in this compilation along with third party links (to
promote). In case some are missed, it is not with malafide intent. Please
email full details to esamskriti108@gmail.com
and we shall effect the change.
To read all
articles by author
To
read all articles on Traditional Indian Textiles of India
Author Trishna
Patnaik
is a self-taught artist based in Mumbai, Trishna has been practising art for over 14 years. She is now a full-time professional painter pursuing her passion to create and explore to the fullest. She conducts painting workshops across India. She is also an art therapist and healer who works with clients on a one to one basis. Not to forget her quality writings on Indian Art and now Textiles for esamskriti. She fancies the art of creative writing.