- Article
covers the handlooms of Gujarat i.e. Patola, Asavali Sarees, Kutch textiles,
Mashru fabric and Tangail Sarees.
The
state of Gujarat in India, popularly known as the Manchester of the East, has a
rich heritage of textile crafts. The arid region of Kutch is the richest in the
state in terms of cultural heritage. However, there are several other parts of
the state which specialize in some form of textile craft or the other. In this
article, we have outlined some of the traditional textile crafts of this
beautiful state.
1. Patola
Elephant, peacock,
parrot, girl & flowers on Patola sari. Credits www.guidetogo.in.
Also Read The
Story of Patola Weaves of Gujarat
2. Asavali Saree
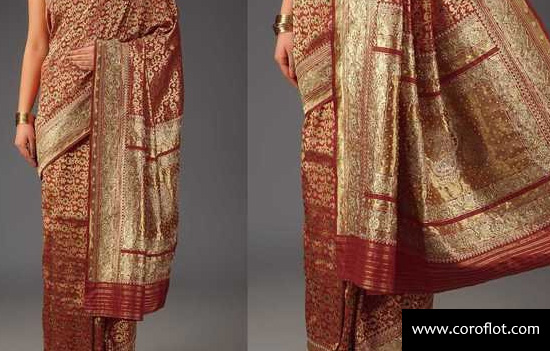
![]()
The Asavali saris named after the old city of Ahmedabad in Gujarat and derive their name from Ahmedabad’s 11th century ruler Asha Bhil. It had rich brocaded patterns woven in twill weave, a speciality of the area. Intricately woven silken patterns were embedded into the gold surface in myriad colours and were known as meenakari, imitating the enamel work prepared on jewellery.
Ashavali
sarees, a style of weaving to which references are found from the 16th century.
Believed by some to have influenced the brocade traditions of
Benaras through the migration of Gujarati weavers, Ashavali fabrics were
made by Khatris and Patels, and used primarily by royalty and nobles. They
were worn as sarees, jamas and patkas, or used for canopies, and
decorations for camels and elephants.
Ashavali
sarees are distinguished by the enamelled look of the border-which are
sometimes woven onto Patola sarees-and the interwoven designs. The
pallu is also very important. Radhika Lalbhai displays designs like the
badshah pallu (common to Balucheri sarees) and chand-tara, and motifs like
the parrot and peacock, some of which are found in other parts of Gujarat
like mocha embroidery, beadwork and jaliwork.
History
Sometime in the late 1930s, a farmer in Ridrol village of Gujarat’s Mansa tehsil thought of learning how to weave brocade sarees using gold and silver threads on silk. Somabhai Patel, who would be free after sowing seeds in the monsoon, wanted to put his time to good use. Many weavers in his village were engaged in weaving. Thus, Somabhai decided to learn the craft.
Over
the years, he developed such a liking for the art that he continued it even
when others in the profession began to quit weaving in the 1980s and 1990s. Just
when the last of the weavers were set to exit the craft, Somabhai set up four
looms, each employing two artisans.
Eighty
years later, his grandson Paresh Patel is continuing the tradition with 55
looms and thirty weavers making Ashavali sarees, characterised by brocade weave
with a variety of motifs including paisley, birds, humans, animals and vines.
Weaving Process
Kinkhab is
made using a thick tano, (vertical thread or warp) or vano (horizontal
thread or weft) in 36 pano (width, measuring 36 inch).
Later, kinkhab began to be used in saree weaving in a 45 or
48 pano.
Initially,
the weaving was done using the jala technique,
which required three craftsmen at a time. The technique gets its name
from jala-a metallic structure atop a loom to which the threads are
attached while their corresponding ends are attached to the warp below. Two
artisans weave and the third one pulls the threads so that designs can be
embossed on the sarees.
However,
the jala technique gave way to the jacquard system, which requires
only two artisans on the loom. In jacquard weaving, the designs are sketched
and then punched into paper cards. Each card corresponds to a row of the
design. These cards make a continuous chain, are fed into the loom and weaving
is done using a shuttle.
The
major difference between jala and jacquard is that the jacquard
instrument is used to pull threads instead of a craftsman.
The
nature of the twill results in the diagonal lines on the textile. These motifs
are then woven with supplementary weft yarns that may be of metal, silk or
other natural fibre yarns.
The
threads are prepared by softening, drying and wrapping them around a spindle.
The loom is prepared based on a carding system that dictates the design.
Uniqueness
The
distinguishing feature of this kind is the circular designs known as butis which are woven into the field in
form of warp instead of the typical weft insertions. It makes the butis appear
horizontal when the saree is worn. The Gujarati brocade is very thick and heavy
thereby it is further enhanced with meenakari work. The rich patterns woven on
the saree appear all the more incredible because of twill weave.
Asavali
sarees are known for their resemblance towards dyes and vibrant colors, high
absorbance, light weight and buoyancy. The aesthetic appeal of the sarees is
enhanced with the use of floral designs in colored silk against gold zari. The
motifs usually has leaves, flowers, stems, outlined by a fine dark line like
inlay work and that is what makes the Gujarati brocade stand out amongst other
brocades.
Credits and useful information
3. Mashru
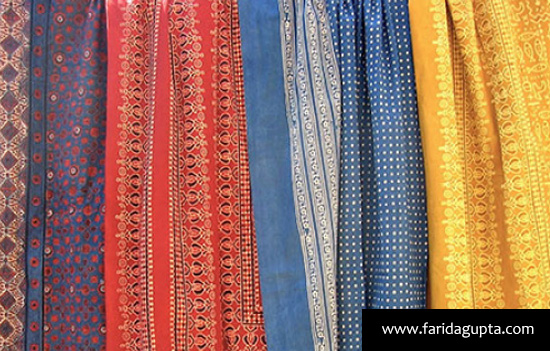
Besides
beautiful embroideries Gujarat is also home to amazing weaves that are a
combination of generations of expertise and skills. Mashru fabric is a hand-woven
mix of cotton and silk. Mashru silk has the appearance of glistening silk that
conceals the soothing feel of cotton. Bright contrasting stripes in vibrant
colors are a characteristic of Mashru fabric.
The
fabric is mainly manufactured in Patan and Mandvi, Gujarat. Mashru fabric has a
satin finish and striped Ikat weave. Mashru sarees and lehengas are an
important part of the bridal trousseau in different communities.
Mashru
has a silk exterior, but the inner fabric which stays in contact with the skin
is made up of cotton. It seems that the makers of this fabric put every
possible color together in lustrous compositions. For the people with a taste
of luxury this blend of the opulence of silk and the comfort of cotton, in
multi-colored stripes and Ikat patterns, is the right choice.
Silk on
the outer surface has a glossy appearance, the cotton yarns on the
back side, soak sweat and keep the wearer feeling cool in warm weather
conditions so fabric has practical use in India. Craftsmen have developed new
designs by tie-dyeing the fabric and using Bandhani technique. Traditionally
used in garments, Mashru is also used for making quilts, cushions and bags.
Making of Mashru
Mashru
fabric is made up of silk and cotton yarns; where silk is used as the vertical
yarn and cotton is used as the horizontal yarn. Each silk yarn goes under the
cotton yarn once, and five or eight time above it. After completing the weaving
of the fabric, it is washed in cold water and is beaten with a wooden hammer
while it is moist.
Natural
vegetable dyes are used to add color to the fabric. Mashru is compressed with
hard press. This weaving technique of Mashru fabric results in a shiny surface
that is identical to silk fabric and comfortable cotton on the inside of the
clothing.
Interweaving
of silk and cotton makes Mashru a durable fabric.
Present day status of Mashru
Recently,
a few craftsmen use chemically dyed rayon instead of pure silk, to reduce the
cost of the final product. Rayon is economical and gives better texture and
shine than silk. However, synthetic dyes that are used now make the fabric
weak. Mashru has now found its place in a range of home furnishings, side
lining the garments.
Designs
of Mashru have become simpler with time. Bright and vivid designs with solid-colored
fabrics are replacing the traditional Ikat designs and patterned stripes.
Craftsmen incorporate Bandhani saree designs with Ikat. Traditional Mashru is
on the brink of extinction. Fabric is being made with power looms today.
Creation of Mashru with cotton and silk yarns, is a dying art form.
Maintenance of Mashru
Mashru
is relatively easier to maintain as compared to pure silk. However, care tips
include, washing this fabric in cold water and slow rinsing. Drying the fabric
in direct sunlight helps in keeping the glossiness of the fabric for a long
time.
Mashru
fabric finds customers all across India. Its colours bring a smile.
Application
The
Mashru fabric was originally used to make apparel such as kurtas and tunics for
men of the Muslim community. When the fabric later spread to Gujarat, women in
the Saurashtra and Kutch regions used the fabric to weave backless Kanjari blouses,
Cholis and vibrant ghagras. They also did embroidery and mirror work to create
their own versions of the fabric. In recent times, Mashru Silk has been revived
by Avant Garde designers through use of contemporary styles.
We
can see patrons starting to prefer Mashru silk for apparel like blouses, where
Mashru fabric provides the perfect mix of the glamor of silk and the comfort of
cotton. Mashru Scarves and Stoles are also becoming popular. They add a
glamorous element to basic everyday outfits.
Everything
you needed to know about Mashru Fabric and Credits
4. Kutch Weaving
Shrujan is a leading NGO of Kutch that has promoted local textiles for decades.
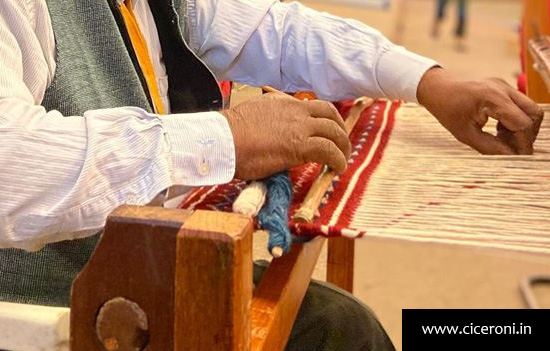
The
traditional Kutch weaving is a 600-year-old tradition. It is done by an
extra-weft weaving technique, where a weft yarn is used in the warp of the
loom. The weaving with extra weft creates the distinctive designs with
geometric patterns. The characteristic, intricately handwoven motifs form the
identity of the Kutch weaving.
Shawls
are woven with motifs. They were originally made from local desi wools and were
traditionally worn as veils. Artisans continue to design and produce shawls for
the local market as their shawls are widely worn throughout Kutch. Over the
years, the weavers spread out in large clusters and smaller pockets throughout
Kutch.
Origin
600
years ago, the Marwadi community from Rajasthan migrated to the Kutch region.
They are known today as Vankar for the art of Traditional Kutch weaving. Traditionally,
weavers used hand-spun cotton yarn provided by the Ahir and Patel farming
communities and wool provided by the Rabari and Jat pastoral communities.
Weaving was then a local art. It provided Kutch communities with blankets,
cloth, and traditional dress.
Historical origins
The
weavers of Kutch claim a 500-year-old history in the region. They are
originally from Rajasthan. There are two stories of their migration.
One
story goes that when a girl of a very rich Rabari family was given in marriage
and came to Kutch, a weaver was included as part of her dowry so that he could
weave the clothes that she would need. This family of weavers gradually grew
into a larger community and spread in different settlements of Kutch.
As
per the second story, Shri Ramdev peer came to Narayan
Sarovar in Kutch on a pilgrimage from Rajasthan. At the time, some
followers who were goldsmiths from Faradi in Mandvi built a temple for him and
requested him to bring his kin from Marwar in Rajasthan for its upkeep. That
was the beginning of the settlement of the Meghwal community of weavers from
Marwar. The community has four sub-communities i.e. Maheshwari, Marwada,
Gurjara and Chaaran. Of these the Maheshwari and Marwada practiced weaving and
leatherwork.
Shyamji Bhai shop, village Bhujodi near Bhuj. Belongs to the Meghwal community.
Thus,
the Meghwal community of Rajasthan migrated to Kutch and brought with them the
art of handloom weaving. Traditionally, weavers used hand spun yarn provided by
Rabaris, a nomadic community of sheep
and goat herders. Kutch weaving is known for its incorporation of distinctive
traditional motifs and colours in medium to heavyweight textiles. The value of
Kutch handlooms lies in the value is created by skilled artisans who weave
their tradition and way of life into each piece.
The rich and diverse creative traditions of Kachchh (often written as “Kutch”) live at the intersection of cultures and communities. The designs woven into Kachchhi woven fabrics were inspired by the communities who wore them, replicating the shapes of musical instruments, the footsteps of an animal herd, etc.
From
morning to dusk, meditatively the music plays on. The spin wheel, the beats of
loom and the birds chirping on vocals. Weavers are closely linked
socioeconomically with their local clients, the Ahirs, Rajputs, and Rabaris.
Each weaver was once personally linked with a Rabari family, who would supply
yarn from sheep and goats. Farming communities like Ahirs cultivated kala
cotton, which produced woven textiles for shoulder cloths and headgear. Sheep
and goat wool was used for veils, skirts, shawls and blankets. The designs
woven into Kachchhi woven fabrics were inspired by the communities who wore
them, replicating the shapes of musical instruments, the footsteps of an animal
herd, etc.
The
names for motifs like vakhiyo, chaumukh, satkani, hathi, or dholki are evocative of rural images. In the 1960’s, cheaper mill made cloth flooded the market and the local market declined. The weavers were forced to look for external clients and shift their practices to fit the demand of larger markets. A group of four enterprising weavers created a Bhujodi Weavers Cooperative which brought together all of the weavers in Bhujodi.
Now
Bhujodi is a popular tourist destination for weaving, though weavers are spread
all over Kachchh.
Village women at work, village Noronha 40 kms from Bhuj.
Today, there are 1200 weavers all across Kutch in 210 villages. The number of women involved in the preparatory and finishing processes is around 2400. Apart from Bhujodi, Vannora, Kota, Jamthara, Sarli, Bhuj, Kadarthi are other villages in Kutch region where weaving happens. Weaving as a process goes around the year apart from the rainy season, when work hits a lean because of practical reasons. Not relying too much on today’s education system, the vankars train their future weavers from a very tender age. Growing around the traditional looms in the household, the kids learn by seeing.
Craft
is to Kutch what beaches are to Goa and Credits
To
see album of Shrujan NGO
, Bhujodi
Weaving products , Craft
Villages Kutch
5. Tangail
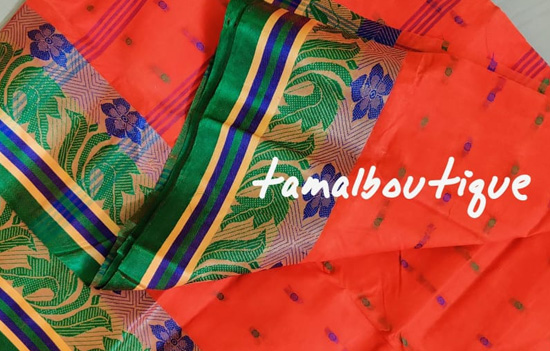
The
crafts persons belonging to the semi-desert land of Rann of Kutch make Dhaba
shawls. The shawls are yarned on the traditional loom using cotton and woollen
yarns. Using threads, a design is put on the loom to shape up the product. The
extracted water of rice or starch is used to wrap the desired colour directly
on the loom. Traditionally colours used are black, yellow, red, orange and
green.
The
number of threads is dependent on the design and are tied with pedals.
Craftsperson carries out weaving the shawls using the up and down technique.
The wool is collected from the sheep and the texture is rough.
Surendarnagar
district in the Saurashtra is the prime location for the Tangail weaving. Loose
and twisted white wool is used to make designs. Two or three warp threads are
involved to give the ready feel of bead- like appearance.
The Tangail is woven traditionally with broad borders featuring lotus, lamp and fish scale motifs. These saris feature highly stylized Jamdani motifs on Tangail fabrics fine textured fabric with 100s count. The traditional Tangail jamdani saree always have a Padma or a lotus paar or a Pradeep or lamp paar unlike the “aansh paar” which is commonly found in other jamdani sarees. Usually a single color is used to design the saree. But these days up to three colors are used in the border of the saree to give it a “Meenakari” effect.
In
Tangails the embroidery thread is inserted after two ground picks. The
main characteristic of Tangails is the extra weft butis, tiny
motifs repeated all over the ground. Tangails are popular and continue to
be woven by weavers as being light, they are excellent for everyday wear esp. in
a tropical country like India.
Credits
Rajkot and Patan weaving traditions not included above.
The
purpose of this compilation is to document and promote. We have given credits
and reference links in this compilation along with third party links (to
promote). In case some are missed, it is not with malafide intent. Please
email full details to esamskriti108@gmail.com
and we shall effect the change.
To read all
articles by author
To
read all articles on Traditional Textiles of India
Author Trishna Patnaik is a self-taught artist based in Mumbai, Trishna has been practising art for over 14 years. She is now a full-time professional painter pursuing her passion to create and explore to the fullest. She conducts painting workshops across India. She is also an art therapist and healer who works with clients on a one to one basis. Not to forget her quality writings on Indian Art and now Textiles for esamskriti. She fancies the art of creative writing.